- Gwint M24 cechuje się dużą wytrzymałością mechaniczną i jest chętnie stosowany w budowie maszyn.
- W porównaniu z gwintami M12 i M14, M24 pozwala na przenoszenie większych obciążeń.
- Gwint M24 jest mniejszy i słabszy od gwintu M20, ale większy i mocniejszy od M22.
- Dobór gwintu M24 vs M20 lub M22 zależy od konkretnego zastosowania.
- Gwint M24 jest dobrym kompromisem pomiędzy wytrzymałością a gabarytami.
Jak wygląda gwint M24
Gwint M24 należy do grupy gwintów metrycznych i ma średnicę zewnętrzną 24 mm. Skok gwintu wynosi dokładnie 3 mm, co oznacza, że na odcinku 1 cala zmieści się dokładnie 8 wzajemnie współpracujących zwojów gwintu. Gwint ten charakteryzuje się symetrią 60°, a więc kąt profilu wynosi 30°. Oznacza to, że dwie ściany profilu gwintu tworzą ze sobą kąt 60°, a każda ze ścian tworzy kąt 30° z osią gwintu.
Gwint M24 należy do grupy gwintów o średnim skoku. Jego zaletą jest duża wytrzymałość przy stosunkowo niedużych gabarytach. Dzięki temu znajduje szerokie zastosowanie w budowie maszyn i urządzeń.
Parametry gwintu M24
Średnica zewnętrzna gwintu M24 wynosi 24 mm, a jego średnica wewnętrzna (rdzenia) to ok. 21 mm. Skok gwintu M24 to 3 mm. Tolerancja gwintu mieści się w zakresie 6g-6H, co oznacza dokładność wykonania. Gwint M24 ma profil trójkątny symetryczny o kącie 60°.
Można spotkać gwint M24 o długości od kilkunastu milimetrów, aż do długości kilkudziesięciu centymetrów. Wszystko zależy od konkretnego zastosowania i wymagań projektowych.
Dlaczego gwint M24 jest popularny
Gwint M24 cieszy się dużą popularnością w przemyśle ze względu na swoje parametry wytrzymałościowe. Jest chętnie stosowany wszędzie tam, gdzie potrzebne są połączenia gwintowe o średniej średnicy i wysokiej wytrzymałości.
Gwint M24 pozwala na przenoszenie dużych sił oraz momentów obrotowych. Jest na tyle mały, że można go stosować w maszynach i urządzeniach o ograniczonych gabarytach. Jednocześnie zapewnia wystarczającą wytrzymałość nawet w trudnych warunkach eksploatacji.
Gwint M24 jest też łatwy w obróbce na tokarkach i frezarkach. Nie wymaga specjalnych, drogich narzędzi. Łatwo znaleźć odpowiednie klucze, nakrętki i inne elementy gwintowe tego typu. To również przekłada się na popularność tego gwintu.Czytaj więcej: Buty i kombinezon motocyklowy turystyczny - Wygodne i funkcjonalne opcje
Porównanie gwintu M24 i M12
Gwint M12 ma średnicę zewnętrzną wynoszącą 12 mm. Jest zatem znacznie mniejszy od gwintu M24. W konsekwencji gwint M12 może przenosić dużo mniejsze obciążenia.
Maksymalny moment dokręcenia dla śruby M12 wynosi ok. 10 Nm. Dla śruby M24 moment ten może sięgać nawet 130 Nm. Oznacza to ponad 10-krotnie większą wytrzymałość gwintu M24.
Gwint M12 stosuje się w połączeniach, gdzie wymagana jest mała średnica i niewielkie obciążenie. Np. w precyzyjnych instrumentach, drobnych mechanizmach, elektronice. Gwint M24 świetnie sprawdza się w budowie maszyn i wszędzie tam, gdzie potrzebne są solidne, wytrzymałe połączenia gwintowe.
Kluczowe różnice między gwintami M12 i M24
- Gwint M12 ma średnicę 12 mm, gwint M24 ma średnicę 24 mm
- Gwint M12 wytrzymuje obciążenie do około 10 Nm, gwint M24 do 130 Nm
- Gwint M12 stosuje się w precyzyjnych mechanizmach, gwint M24 w budowie maszyn
Porównanie gwintu M24 i M14
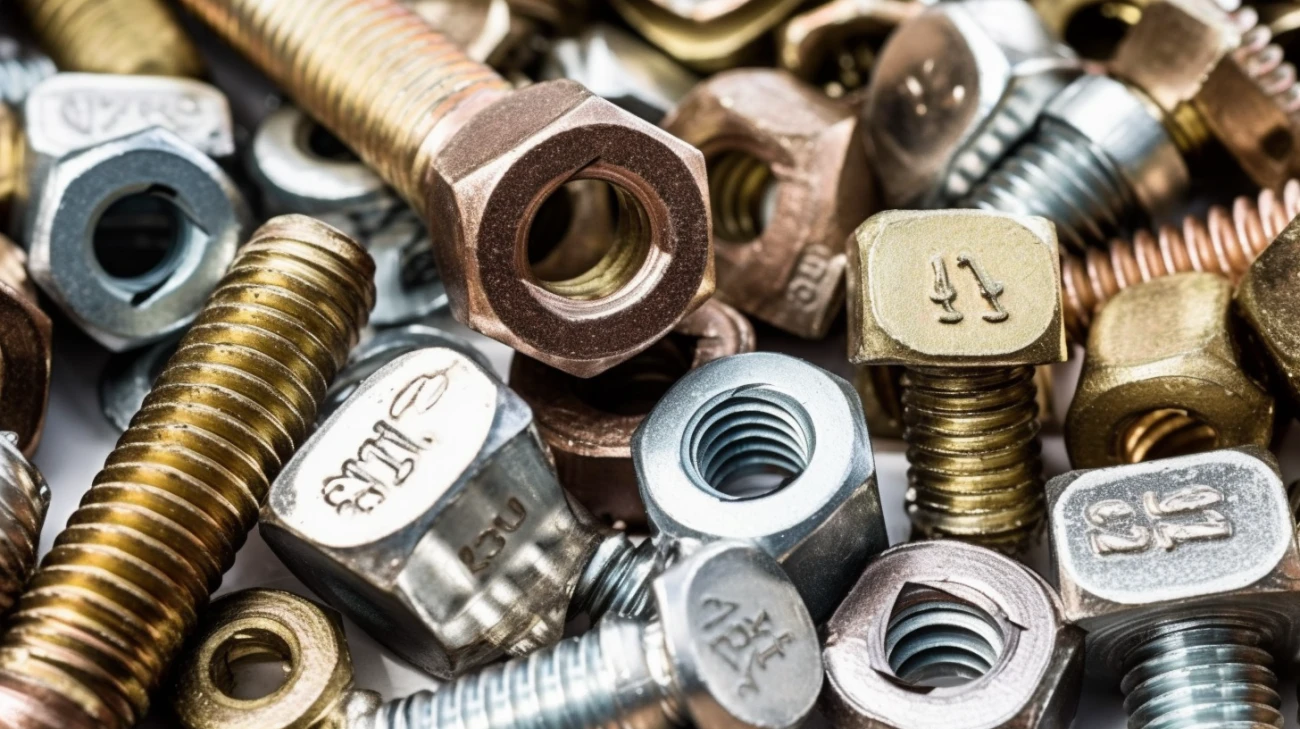
Gwint M14 ma średnicę 14 mm, czyli pośrednią między gwintami M12 i M24. Pod względem wytrzymałości gwint M14 plasuje się mniej więcej w połowie skali między M12 i M24.
Maksymalny moment dokręcenia dla śruby M14 może sięgać około 20 Nm. Jest więc wyraźnie mocniejszy od gwintu M12, ale słabszy od popularnego gwintu M24.
Gwint M14 stosuje się tam, gdzie wymagana jest większa wytrzymałość niż zapewnia gwint M12, ale nie potrzeba aż tak dużej sztywności jak w przypadku gwintu M24. Gwint M14 sprawdza się w połączeniach o średnim obciążeniu np. w mechanizmach precyzyjnych.
Kluczowe różnice między gwintami M14 i M24
- Gwint M14 ma średnicę 14 mm, gwint M24 ma 24 mm
- Gwint M14 wytrzymuje do ok. 20 Nm, gwint M24 do 130 Nm
- Gwint M14 w mechanizmach precyzyjnych, gwint M24 w maszynach
Porównanie gwintu M24 i M20
Gwint M20 charakteryzuje się średnicą zewnętrzną równą 20 mm. Jest więc nieco mniejszy od gwintu M24. W konsekwencji gwint M20 jest też nieco słabszy od gwintu M24.
Maksymalny moment dokręcenia dla śruby M20 wynosi około 100 Nm. Dla gwintu M24 jest to 130 Nm. Różnica ta przekłada się na mniejszą sztywność i wytrzymałość połączeń z gwintami M20 względem gwintów M24.
Gwint M20 stosuje się wszędzie tam, gdzie wymagana jest duża wytrzymałość połączeń gwintowych przy nieco mniejszych gabarytach niż zapewnia gwint M24. Dobrym przykładem są ramy rowerowe.
Kluczowe różnice między gwintami M20 i M24
- Gwint M20 ma średnicę 20 mm, gwint M24 ma 24 mm
- Gwint M20 wytrzymuje do ok. 100 Nm, gwint M24 do 130 Nm
- Gwint M20 w rowerach, gwint M24 w maszynach
Porównanie gwintu M24 i M22
Gwint M22 ma średnicę 22 mm, czyli minimalnie mniejszą od popularnego gwintu M24. Pod względem wytrzymałości oba gwinty są do siebie zbliżone.
Dla gwintu M22 maksymalny moment dokręcenia wynosi około 120 Nm. Jest więc tylko nieznacznie mniejszy od 130 Nm dla gwintu M24. Oba gwinty mają zbliżoną sztywność i parametry wytrzymałościowe.
Wybór pomiędzy gwintami M22 i M24 zależy od konkretnego zastosowania i wymagań projektowych. Gwint M24 dzięki większej średnicy pozwala na przenoszenie nieco większych obciążeń.
Kluczowe różnice między gwintami M22 i M24
Średnica zewnętrzna | Gwint M22: 22 mm | Gwint M24: 24 mm |
Maksymalny moment dokręcenia | Gwint M22: ok. 120 Nm | Gwint M24: ok. 130 Nm |
Podsumowanie
Gwint M24 to popularny gwint metryczny o średnicy 24 mm. Odznacza się dużą wytrzymałością i sztywnością, dlatego znajduje szerokie zastosowanie w budowie maszyn i urządzeń. W porównaniu z mniejszymi gwintami M12, M14 czy M20, gwint M24 pozwala na wyższe obciążenia i momenty dokręcenia. Jednocześnie gwint M24 ma nieco mniejsze gabaryty i lepszą wytrzymałość niż gwint M22. Dzięki temu jest chętnie stosowany wszędzie tam, gdzie liczy się zarówno kompaktowa budowa, jak i wysoka sztywność połączeń gwintowych.
Gwinty metryczne, takie jak M12, M14, M20, M22 czy M24, są powszechnie stosowane w budowie maszyn i urządzeń. Każdy z tych gwintów ma swoje typowe zastosowania, wynikające z gabarytów i wytrzymałości. Gwint M12 ze względu na małą średnicę sprawdza się w precyzyjnych mechanizmach i elektronice. Z kolei gwint M24, dzięki dużej wytrzymałości, jest chętnie wykorzystywany w konstrukcjach nośnych maszyn.
Wybór konkretnego gwintu M12, M14, M20 czy M24 zależy od wymagań projektowych dla danego połączenia lub zespołu. Im większe obciążenia występują, tym większy i mocniejszy gwint należy zastosować. Gwint M24 ze względu na optymalne połączenie gabarytów i wytrzymałości jest chętnie stosowany w budowie maszyn.
Porównując ze sobą gwinty M12, M14, M20, M22 i M24 warto zwrócić uwagę na takie parametry jak średnica zewnętrzna i wytrzymałość na moment skręcający. Im większa średnica i wytrzymałość gwintu, tym większe obciążenia może on przenosić. To determinuje dobór odpowiedniego gwintu do danego zastosowania.
Gwinty metryczne są uniwersalne i powszechnie dostępne. Dzięki bogatej ofercie wielkości i wytrzymałości z łatwością można dobrać optymalny gwint do konkretnych wymagań projektowych. Umiejętny dobór gwintów M12, M14, M20, M22 czy M24 pozwala na budowę wytrzymałych i niezawodnych maszyn i urządzeń.